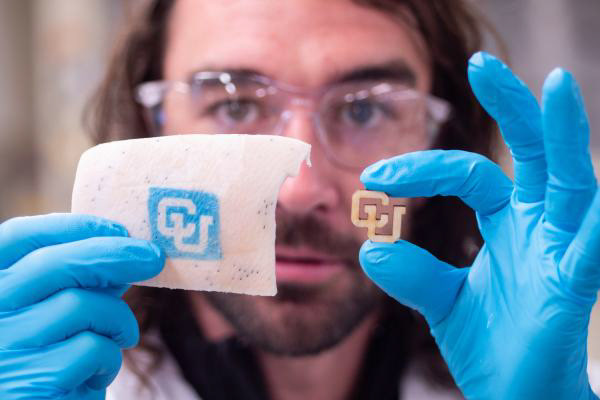
I met with Dr. Bruns to gather some tips and pointers when working with epoxy resins as he has experience working with the material. Although he hasn't made anything quite as deep & thick as my project, he was still able to give me some very useful information and creative application suggestions.
Carson confirmed my suspicions that you shouldn't pour the resin any deeper than 1/4 inch at a time due to the excessive heat which can form from having too much mass reacting at the same time. I've experienced this in my prototyping as more air bubbles are released from the wood pieces the hotter it gets. When I asked him about the best methods for removing the escaping air bubbles he noted a blow torch to be the best option. Additionally, he recommended carefully clearing out the bubbles and maybe leave small patches or rivers of bubbles to give an underwater oceanic effect.
There were some questions pertaining to materials I can use when making a casting mold, Carson informed me that any hydrophobic plastic should be fine. Polycarbonate would Not work, but polyethylene or something similar shouldn't bond to the epoxy as it dries. And to adhere pieces to the structure prior to pouring (shells, plastic trash, etc,) I should use a quick dry epoxy.
Carson was able to confirm much of what I gathered from my research, and clarified some of my unknowns. Aside from that, the project is coming along nicely and he looks forward to the finished product!